連載:第9回 成長企業 社長が考えていること
大手からの開発パートナー指名は「長い〇〇」のおかげ。中小製造業、正しい枠のはみ出し方
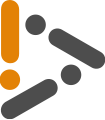

東京・八王子市で約50年。板金加工の下請けから始まった菊池製作所は、今や大手各社から「試作・製品開発パートナー」としての厚い信頼を得るまでになりました。近年はマッスルスーツやサービスロボットなどの製品の創出を大学ならびにスタートアップとともに進め、シルバー向け製品を中心としたサービス・サポート系ロボットの開発メーカーとしても注目を集めています。なぜ、同社には大手企業からの相談が舞い込むのか? どうやってそのような企業に育て上げたのか? 創業社長の菊地功氏に話を聞きました。

株式会社 菊池製作所
代表取締役社長 菊池 功さん
福島県飯館村出身。中学卒業後、東京都新宿に本社を置くカメラの試作品メーカーに就職。1970年に独立・個人創業し、1976年に株式会社菊池製作所を設立。1984年には出身地の飯館村に工場を設立し、故郷に錦を飾る。2011年には株式会社菊池製作所がジャスダックに上場。モットーは、出会いを大切に。
「試作」とは、理想を完璧に具現化する作業
――貴社は大企業からの共同開発や試作についての相談が多いとのこと。どのような強みがあるのでしょうか?
菊池功氏(以下、菊池): 大きくは2つあると思っています。1つは、当社が『高精度・高品質な試作品の製作から量産化までを、1社で完結できる一括一貫体制を保有している』こと。もう1つは、当社にご相談いただくことで『連携している47大学、61の研究室のアイデアやスキルを活用できる産学連携ネットワークを保有している』ことです。
このような体制をもつ企業は、なかなか無いかと思います。
――1つずつ伺っていきます。まず、貴社の試作品製作について教えてください。
菊池: よく誤解されるポイントではあるのですが、当社が行っている“試作”は「とりあえず、試しに作ってみる」というものではありません。製品の設計思想・コンセプトを“完璧に再現”した最終製品を生み出す作業。「最高品質・最高精度を追求」することと同義です。
というのも、取引先である大企業をはじめとして、当社に寄せられる試作・開発案件は、高機能な最終製品の「量産」を見据えています。その開発工程では、まず「最高の、完璧な試作品」を作り上げ、そこから市場のニーズに応える機能要件、価格要件を満たすよう、設計や製造法、材料を調整する作業を繰り返していきます。そうやって過剰品質がそぎ落とされ、製造・販売コストがクリアされたものが「量産品」として市場に出回っているのです。
「部品を試しに作ってみる」とは、『試作』の意味合いが大きく異なります。
――設計思想を完璧に具現化した最終製品を製作できる、というわけですね。
菊池: そうですね。完璧……と言い切ってしまうと語弊がありますが(笑)。ものづくりに関係される方にはご理解いただけるかと思います。
例えば最近当社が製造を手掛けていた「マッスルスーツ」や「ドローン」などの高機能製品・最終製品をとりあえず「試作」しようとしても、1社で完結できる企業はなかなかありません。
全体の設計はもちろん、当社の主力事業分野である金属やプラスチック・繊維の加工、加えてセンサ・回路・プログラミングをはじめとした制御系、さらには動力系や操作まわりのインターフェースまで、手掛けるべき作業は広範で膨大です。しかも、量産時の工程まで見据えなければなりません。
さらに言えば当社は「市場のニーズを考慮して、設計・製品に反映させる」ということまでこだわります。これは、下請けとして「与えられた設計図通りに作る」こととは別次元の仕事になります。
――なぜ、そこまでできるのでしょうか?
菊池: 一言で答えるなら「社員力」と言いたいですね。もう少し具体的に言うと「社員の多能工化・情報収集力」の成果です。もちろん、この状況はある日突然できたわけではありません。
当社はここ八王子で1970年に創業し、2020年に50周年を迎えます。設立当初は、板金加工や金型製作を手掛ける小さな町工場でした。周辺には製造業の大手メーカーが数多くあり、そういった企業の「下請けの一社」としてスタートしたわけです。よくある話かと思います。
当社を含め下請け企業の多くは基本的に、メーカーの要望に応える形で得意分野の「専門性」が高まっていきます。この「専門性」の取り扱いが、中小企業にとっては実は厄介なんです。
というのも、中小企業は短期的な売上・利益を重視しがちです。どうしても、資金繰りが厳しいので。専門性を活かせる仕事を受注しようとするのは理にかなったことですし、その繰り返しでいつしか「専門家」と呼ばれるようになるわけです。
しかしこの「専門家」という呼称は逆に言えば、「その仕事以外できない」という評価にも繋がりますし、社内の意識もそちらに向いていきます。当社でいえば、「板金加工・金型製作の専門家」で留まっていた可能性もあるわけです。
単一分野の「専門家」では、モチベーションが続かなかった
金型製作から成形、プレス加工、機械加工など、製品開発を1社で完結できる。
――なぜ、貴社はそうならなかったのでしょうか?
菊池: 一つの仕事だけだと飽きてしまった……あ、私や社員のモチベーションが続かなかった……。いや、「好奇心が抑えられなかった」と言ったほうが綺麗なエピソードになるかもしれません(笑)。
当社が創業した八王子周囲には大手メーカーがたくさんあり、面白そうな案件、興味を掻き立てられる情報が日々やり取りされていました。我々は板金加工・金型製作だけではなく、もっと色々な「ものづくり」がしたかったのです。そして、それができそうな環境が目の前にある。これは……行くしかないでしょう!
我々の経験・スキルでは難しそうな案件も取りに行きました。「もうちょっとがんばればできそうだな…」といった案件を「やらせてほしい!」と提案する感覚です。当然、設備投資も必要になります。短期的な利益を重視していてはできない投資・決断もありましたが、それよりも私や社員のモチベーションのほうが大事でした。こういった設備投資は未来の案件にもつながりますし、新しい機械を導入してそれを使いこなし、やれることが増えていくのはエンジニアとして純粋に楽しいことでもあります。
それらを一つ一つ形にしながら、10年20年の時間が経った結果、ベテランの技術者が育ち、現在の「多能工」や「一括一貫体制」といった現在に通じる強み、企業文化が醸成されていきました。すると大企業との関係も、設計通りのものを製造する「下請け」から「開発パートナー」に変化していったのです。
きっかけは「面白そう!やってみたい!」という漠然とした好奇心だったのかもしれません。ただ、この「好奇心」が持続した結果、今では当社の採用ページにも記載するほど大切なものになりました。当社の社員教育で取り組んでいるジョブローテーションや多様な分野のプロジェクト参画なども、そこが出発点です。
「多能工」につながる “少し”チャレンジングな案件の受注と、それができる設備投資、環境整備。これを続けることが、当社のスタッフやエンジニアを良い意味で飽きさせず、モチベーションを高く維持できる仕組みになっていったのだと思います。私もそうですが、結局はものづくりが楽しいんですよね。
50年先を見る「長い目」。中小企業にない視点は大学にあった
――貴社への相談が多いもう一つの理由、『大学のアイデアを活用できる』点についてはいかがでしょうか?
菊池: これも長年の積み重ねの話になります。大学の研究室と良好なパートナーシップを組めていることが大きな理由ですね。当社では、お客様から製品開発の相談を受けた場合に、47大学61の研究室に、気軽に相談ができ、アイデアや解決法を議論しています。これもまた、当社独自の価値だと思います。
はじまりは、20年以上前に「最終製品のアイデアはどこにあるか?」という問いの答えを、知人の勧めで大学に求めたことでした。我々は「下請け」ではなく、お客様と一緒に製品を開発していく立場でしたので、市場ニーズの把握や時代の先読み、製品アイデアを持つことは必須だと考えたのです。
この記事についてコメント({{ getTotalCommentCount() }})
{{selectedUser.name}}
{{selectedUser.company_name}} {{selectedUser.position_name}}
{{selectedUser.comment}}
{{selectedUser.introduction}}